How to Build a World-Class Manufacturing Facility
/Petrochemical plant in India commits to superior maintenance and forward-thinking processes to build a world-class program and accelerate efficient operations.
By Michelle Segrest, Navigate Content - Reporting for Maintenance Technology Magazine
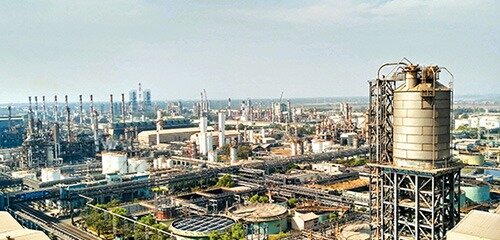
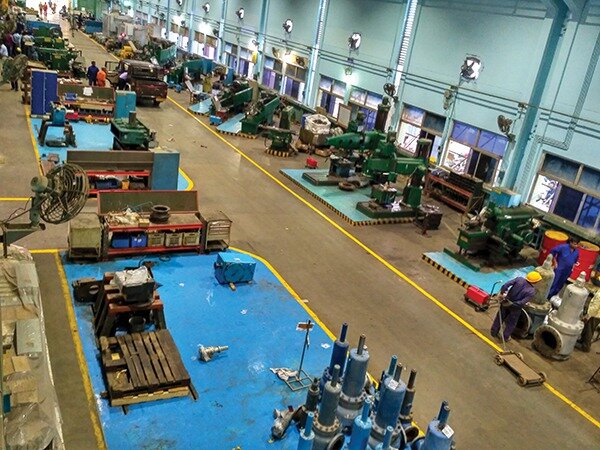
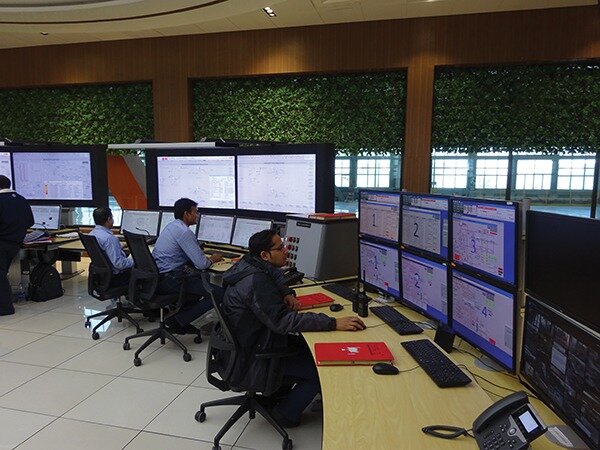
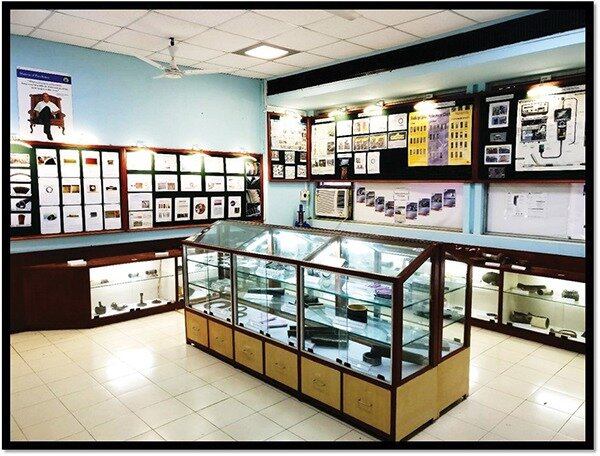
Enter the gates of the Reliance Industries Limited (RIL) Hazira manufacturing division site in Gujarat, India, to find perfectly manicured landscaping with lush trees, bright-green lawns, and flower beds containing thousands of daisies, basoras, ixoras, petunias, and other varieties decorating the entire 1,000-acre campus.
Though visitors may feel as if they are at an exclusive vacation resort, deep within the beauty of the grounds serious manufacturing is at work. Twenty-seven individual chemical and petrochemical plants operate above capacity and with superior maintenance 24 hours a day, seven days a week. It’s also the home of the Foundation for Industrial Maintenance Excellence (FIME) 2017 North American Maintenance Excellence Award winner.
Located on Surat Hazira highway, just 250 kilometers from Mumbai, the 29-year-old facility looks brand new and operates at 390 MW with state-of-the-art equipment, technology, and automation. To keep this kind of facility operating at full speed requires world-class maintenance.
“We take great pride in our manufacturing excellence and our ability to continually improve,” said RIL-Hazira site maintenance manager Kamath Chaitanya. “It has been part of our culture. Each person who works here focuses on growth and improvement.”
RIL reliability engineer Adhara Modi agrees with and emphasizes that sentiment. “When it comes to our commitment to reliability, we aim for the stars and reach the moon,” she added.
The beautiful scenery cannot fully camouflage the high-capacity manufacturing that includes more than 4,000 pumps, more than 250 compressors, 15 turbines, 11,000 control valves, more than 8,000 motors, and more than 92,000 field instruments.
All of this equipment, and more, is maintained at a superior level, according to FIME board members Kyle Braswell and Mark Downing, both former Dupont reliability and maintenance experts, who recently toured and evaluated the facility’s maintenance programs for the NAME-award competition.
For Braswell, his first impression was impactful. He referred to the famous Solomon benchmarking study on maintenance and reliability (RAM), which proves that the age of a facility is no indicator of poor reliability or high maintenance cost.
“I’ve always believed this because the data shows it, but in my more than 40 years in this business, I’ve never actually seen it,” Braswell said. “I walked into this facility, which was built in 1989, and this is the first time I truly saw proof of the Solomon data. These [maintenance professionals] have maintained the facility correctly all along. They are smart enough to know that it is costing them no more to maintain that facility at high reliability than it costs to maintain a new facility. This is proof that age is not a determining factor for cost, reliability, and production capability.”
The RIL-Hazira team achieves this with 80% predictive and preventive maintenance, drones to monitor safety and inspections, exhaustive mounds of documentation, an extensive employee reward and recognition program, comprehensive training for engineers and contract technicians, community outreach, and a unique Corrosion Museum that contains samples and information about any failure that has ever occurred at the site.
Leadership’s commitment to reliability also plays a key role in the success of the facility, Braswell said. “When they incorporate a new project, they are very good at analyzing how that project affects reliability. Reliability is a very clear discussion point in all projects. To commit to it, you have to understand it. Leadership understands maintenance and reliability’s impact on production capability.”
Quest for World-Class Manufacturing Reliability
In an effort to benchmark the facility’s standards against the world’s best, RIL-Hazira reached out to the FIME organization for consideration of the prestigious NAME Award. Even though the award recognizes North American facilities, FIME agreed to evaluate RIL-Hazira.
“We feel like we have a good standard of reliability and engineering and wanted to benchmark our performance to see how it measured with world-class sites,” Chaitanya said. “There are very few agencies in the world that benchmark maintenance. If you look at the global scenario for the past couple of years, there has been a huge variation in crude prices. The way to stay alive in this competitive global petrochemical market is to cut down on production and operating costs. One of the critical aspects is the maintenance of fixed costs. It is essential that we have high levels of productivity. We looked at ways to bring in new technologies that would be cost effective without reducing quality in such a competitive market.”
The extensive evaluation process rated the facility with significantly high scores, according to Downing. “These are some of the highest scores we’ve seen,” he said. “When we got there, we found they had actually under-represented some of their performance. Some things they thought were a weakness were actually some of their strengths. For example, they have only 3% to 5% turnover, and this is extraordinary.”
Maintenance Team for a World-Class Manufacturing Facility
The facility’s maintenance team consists of 450 dedicated professionals and is organized under different heads of engineering and maintenance—mechanical, electrical, automation, civil, minor projects, and administrative.
“We are constantly buying new equipment so we must ensure that our people are trained to maintain these properly,” Chaitanya said. “We have extensive training programs. We have a wide variety, with offerings for new employees to some with 25 to 30 years of experience. Many employees are also cross-trained by moving across disciplines.”
The team utilizes a combination of predictive, preventive, and corrective maintenance approaches based on ACA analysis with an 8×8 matrix that is executed on an SAP platform. This shows the consequences of failures and many other data metrics. Most critical is condition monitoring of all the rotating equipment, Chaitanya said. The team performs 60 to 70 preventive maintenance orders per week per plant, which they consider a key to keeping the machines running efficiently.
Engineers are responsible for the technology and training of the maintenance tech-nicians, who are 100% outside contractors.
“Engineers determine the inspection methodology, but the inspection is contracted to other people,” Braswell explained. “The Hazira engineer lines out the work and training on how to do the work. They have a third party assessing and evaluating the capability of every contract mechanic on the plant site. Here there would be co-employment concerns. Over there, they give all contractors the same health checkups and benefits they give their own employees. These kinds of things just naturally translate to high-quality work.”
Workforce Training Improves Manufacturing Standard
The first 12 months of employment for new engineers involves a comprehensive cross-training program.
A maintenance engineer within one of the units will cross-train with production, electrical, instrument, and materials engineers.
“They cross-train with all the different engineering disciplines to help them understand how the work they are doing integrates with the other engineering disciplines and with the production unit that they are supporting,” Braswell said. “This gives the engineers a strong footing. I haven’t seen this level of cross-training anywhere else.”
Engineers also are trained on how to maintain the equipment. Engineers train the contract mechanics. “At most facilities, the mechanics know how to repair the equipment, but the engineers do not,” Braswell added. “Engineers then follow the work in the field. The engineer gives the lineup for repair to the mechanic, and the engineer follows the work to ensure repairs are made in a quality way.”
Contracted maintenance workers at the facility are treated like employees. Engineers work with the craftsmen and are involved in training and know how to operate the equipment.
“The training and assessment processes are used for their own engineers and the contracted craftsmen,” Downing said. “There is a lot of good teamwork and good communication. Management takes a lot of effort to make these things happen.”
Incentives and Recognition Improves Manufacturing Reliability
At RIL-Hazira, management supports a robust incentive and recognition program.
“The workforce is very eager to get involved to come up with solutions, even for small improvement projects,” Downing said. “Management supports inspiring and recognizing quality all year long. It’s not just a flavor of the month. The Indian government has a recognition process as well. The site participates in this, and they have a winner who actually received an award from the prime minister for a project on site. That’s like the U.S. President hand-delivering an award to a mechanic for a project. India is a country that is trying really hard to make some improvements, and Reliance is a very significant player in all of that.”
The recognition is important in an area where not everything looks like the beautifully landscaped facility inside the RIL-Hazira gates. “When you drive outside of the facility you see everything in a state of disrepair,” Braswell said. “Advanced technology is being used to build roadways, but you still see people carrying concrete on top of their heads. It’s amazing to take people growing up in that environment and train them to maintain and operate a world-class facility. Studies show that 60% of failures come from how we operate the equipment. RIL does a fantastic job of training people who grew up in a simple environment to embrace and use technology and high reliability.”
RIL leadership also strongly encourages innovation. They give engineers time to look for new ways of doing things. “They take the time to research to find new ways to maintain the equipment,” Braswell said. “They invest in people to search for improvements, evaluate them, and implement them, and then people are rewarded and given the time to do it. Leadership recognizes that engineers enjoy doing that and gain a lot of personal satisfaction from doing that. Leadership understands that and rewards this kind of behavior.”
Leadership also recognizes that not everything that is researched and tried is going to be successful. They never penalize someone for something that is researched but not used.
“They recognize there will be hits and misses,” Braswell said. “They learn from the misses and keep going. Mark and I asked the plant manager what he did to develop this kind of culture. He said it’s just how it’s always been. It’s how they grew up. Kamath, the lead maintenance manager, is a very strong leader. It is clear the organization respects him. He knows the technology and holds the organization to very high expectations. Leadership values reliability and maintenance. Operations leadership understands the relationship between reliability and maintenance and good production.”
RIL-Hazira takes the incentive program one step further. “This is a company that values its people,” Braswell said. “But it’s not just them; it’s also their families. There is a medical facility on site. Mammograms are given for women employees and mothers of employees. Stress tests for employees are also given to the parents of employees. The family develops a feeling they are cared for, and a loyalty develops. The company sends medical vans out to the villages for health checks, which develops good will within the community. When you have this kind of loyalty, people want to do a good job.”
RIL-Hazira considers its people to be its greatest asset, Chaitanya said. “We have a very wide and well-established recognition program for motivating people. We recognize people on their efforts and on their ideas. Our people are driven by key performance indicators (KPIs). We have cross-functional teams to help solve problems. We have teams responsible for quality control. All of the groups work on our continual improvement goals with high motivation.”
RIL — A World-Class Manufacturing Philosophy
RIL-Hazira incorporates a wide array of reliability and maintenance programs, including FEMA, RCA, SIL, QCC, and CFT. What makes the reliability and maintenance programs at this site unique is the focus on maintenance excellence, Chaitanya stated.
“The aim of this team is continual improvement toward perfection in every aspect of maintenance,” he said. “Each member of our team is continuously focused on how to improve. The first goal is no breakdowns. Each failure is analyzed to the level of how can we prevent this from happening again. We ensure that people are trained to not only fix problems but to prevent them from recurring. We also want to stay on top of advanced technology, which is always changing. We have a team that works on smart manufacturing with the newest technology like drones, wireless monitoring, mobile apps, and many items which fall under the Internet of Things.”
RIL-Hazira incorporates several maintenance best practices, including shutdown management, SMP, integration of business processes, daily planning meetings, SAP-controlled maintenance work orders, failure analysis, planning and scheduling, and field studies.
Corrosion Museum Improves Manufacturing Operations
A unique tool at the site is its Corrosion Museum. “This is used for training, but it is also a part of our legacy,” Chaitanya said. “We have preserved examples of all of the failures that have happened on site. The failed equipment is displayed and we show the failure, why it happened, and what we did to correct it. All of it is recorded. This helps us to learn how to fix these problems and prevent them from happening again. If we have a problem on the floor, we can go to the Corrosion Museum to see if we had a similar failure that will teach us something. It is a complete history. Anyone in the facility to can go in, find a similar issue, and discover how the problem was solved. There are also examples of the raw metals and resins. There is also documentation for each issue. All these are in digitized format with a user-friendly interface.”
Extensive analysis is part of this preservation, Modi added. “It is very important to me that the uptime is maintained,” she explained. “We take each failure seriously and do a complete analysis. For example, we found a very basic technical mistake in one of our plants. I gave a recommendation to the plant, and this was communicated across the entire site. This alerts the other plants that similar issues can occur. Having this information can help to prevent the same problem at the other plants.”
In the Corrosion Museum, all physical evidence of the failure is displayed in beautiful cases, Downing said. Each has a barcode, and there is a corresponding mobile app that scans the barcode and then reveals the full history and reports the failure, how it failed, how it was repaired, and how it can be prevented. The displays include piping, pump impellers, valves, and other equipment.
“We found this to be amazing because when you are doing a failure analysis but haven’t seen any of these mechanisms before or the results of failure, it’s hard to do a really good failure-mode-and-effect analysis,” Braswell said. “Engineers, operators, mechanics…anyone can go through and learn based on previous failures at the plant.”
This enhances the company’s commitment to maintenance, Braswell added. “If you properly maintain your equipment, it doesn’t cost more as time goes on, and you don’t lose your reliability. Many people think old equipment equals poor reliability. It doesn’t have to be that way. If you maintain it effectively, you actually save money down the road. It costs a whole lot more money to replace a piece of equipment than it does to maintain it correctly. It takes clear leadership direction and holding people accountable.”
Documentation Improves Manufacturing Processes
Another impressive feature of the maintenance efforts at RIL-Hazira is the level of documentation that is recorded and made available.
“We believe that you should not keep reinventing the wheel,” Chaitanya said. “You have to learn from mistakes. It is essential that we document all the things that we do, successes and failures. We have about 1.7 million documents on our documentation platform. Any person on the site, at the switch of a button on their laptops, can access any of these documents.”
Company-wide documentation ensures that all Reliance plant sites follow the same documentation process. Much of the documentation is in the SAP system. Almost every job has a long, written procedure.
“This is a company that leverages learning as broadly as possible,” Braswell said. “They have a corporate group that creates a lot of the maintenance training procedures. Procedures are standard across all facilities. They are very good about leveraging best practices within the plant and across other plant sites. Their turnaround documentation is phenomenal, with big books on how the turnaround was executed, what was learned, the schedule, and the maintenance performed. They continue to work to improve this. There is an extensive history of everything, and there is easy access to it from anywhere.”
Drones Used in Manufacturing
RIL-Hazira uses drones to do inspections at heights of 72 meters. These drones also help to monitor safety.
Health and safety in the petrochemical industry is recognized by the department’s vision to ensure safe performance, demonstrating the personal commitment to safety, engaging people in decision making, and being transparent when dealing with HSEF (health, safety, environmental, and fire) concerns.
“The maintenance practices that aid in technology always make some innovative approaches for operation reliability and system safety,” Chaitanya said. “Remote visual inspection is one such technology that enables us to reach the goal of operational reliability with the highest attainable safety. Remote visual inspection is an indirect, nondestructive technique that employs drones to deliver clear, concise, and current visual data.”
The use of drones permits remote visual inspection of flare stacks, tall towers, chimneys, and structures with ease in an otherwise difficult height and environment where waves, wind, and weather place further demands on the individuals inspecting an asset, Chaitanya explained.
“Inspection using drones negates the need of long scaffolds, and it offers a monitoring program for observations. It also reduces the breakdown situations through timely identification and evaluation of condition by planned schedules.”
Community Outreach Contributes to World-Class Manufacturing
It is important to RIL management to do all they can to help build the surrounding communities. A notable example is a hospital they recently built, primarily to treat AIDS patients. There is also an emergency vehicle that patrols the area, providing medical checks and medicine to residents in the nearby villages. RIL-Hazira continues to meet India’s environmental regulatory requirements.
“The organization is very concerned with the people of India and very focused on improving India,” Downing said.
He pointed to several examples of RIL’s projects:
A “Cancer Awareness and Prevention Campaign” covered all sites. The campaign shared information on early detection through screening and provided cancer-prevention tips.
A leading gynecologist had an interactive session on cervical cancer and its prevention for women employees.
Interactive sessions were held on “Healthy Diet for Heart.” Another session that emphasized the need to keep the body fit involved demonstrating stretching exercises that could be performed in offices.
A session for contract workers on lifestyle management was conducted.
A self-defense training course for women employees was organized in coordination with the Hazira Women Council.
Truck and tanker drivers were trained in “Defensive Driving Techniques” at DSTC (Drivers Safety Training Centre) in Hazira. As part of the safety initiative, the company established a Truckers’ Safety Training Centre at Hazira. This center is fully equipped with audio-video equipment to impart training to truck drivers on safety rules, efficient driving techniques, and emergency responses. More than 243,000 drivers have been trained through this initiative since its inception in 2005.
“RIL has always aimed higher and committed to sustainable development that goes beyond our operating boundaries,” Chaitanya said. “The continuous development has led us to grow into a more evolved organization in terms of the way we select our projects. As we have been evolving over the years, so have our processes. All of our projects undergo critical and stringent selection criteria, and projects with a sustainability focus or a socio-ecological focus are undertaken. The impact that our projects have on the economic development, product development, society, and natural environment plays a major role in their selection and is in line with our evolution into the sustainable business environment.”
The NAME Award for Manufacturing Excellence
The Reliance Industries Limited (RIL) Hazira manufacturing division site in Gujarat, India, is the 2017 Foundation for Industrial Maintenance Excellence (FIME) North American Maintenance Excellence Award winner. The NAME Award (nameaward.com) recognizes organizations that excel in reliability and maintenance practices that enable operational excellence.
Objectives of the award program are to:
Increase the awareness of maintenance as a competitive edge in cost, quality, service, and equipment performance.
Identify industry leaders, along with potential or future leaders, and highlight “best” practices in maintenance management.
Share successful maintenance strategies and the benefits derived from implementation.
Understand the need for managing change and stages of development to achieve maintenance excellence.
Original version published in Maintenance Technology, February 2017
Updated October 2019
If you like this article about building a world-class manufacturing facility, please PIN IT!
This page contains affiliate links. If you click on the product links and make a purchase, it allows me to make a small commission at no extra cost to you! Thank you for your support and I hope you find value in this content!