How to Develop an Effective Maintenance and Reliability Strategy
/Building an effective strategy is the first step in developing and implementing crucial maintenance and reliability programs. Clinton Davis shows how his team created an effective maintenance and reliability overhaul for a major water utility in Georgia.
By Michelle Segrest, Navigate Content, Inc. — Reporting for Maintenance Technology Magazine
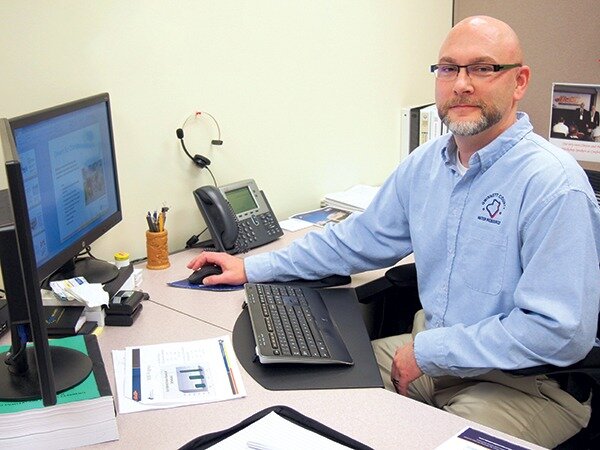
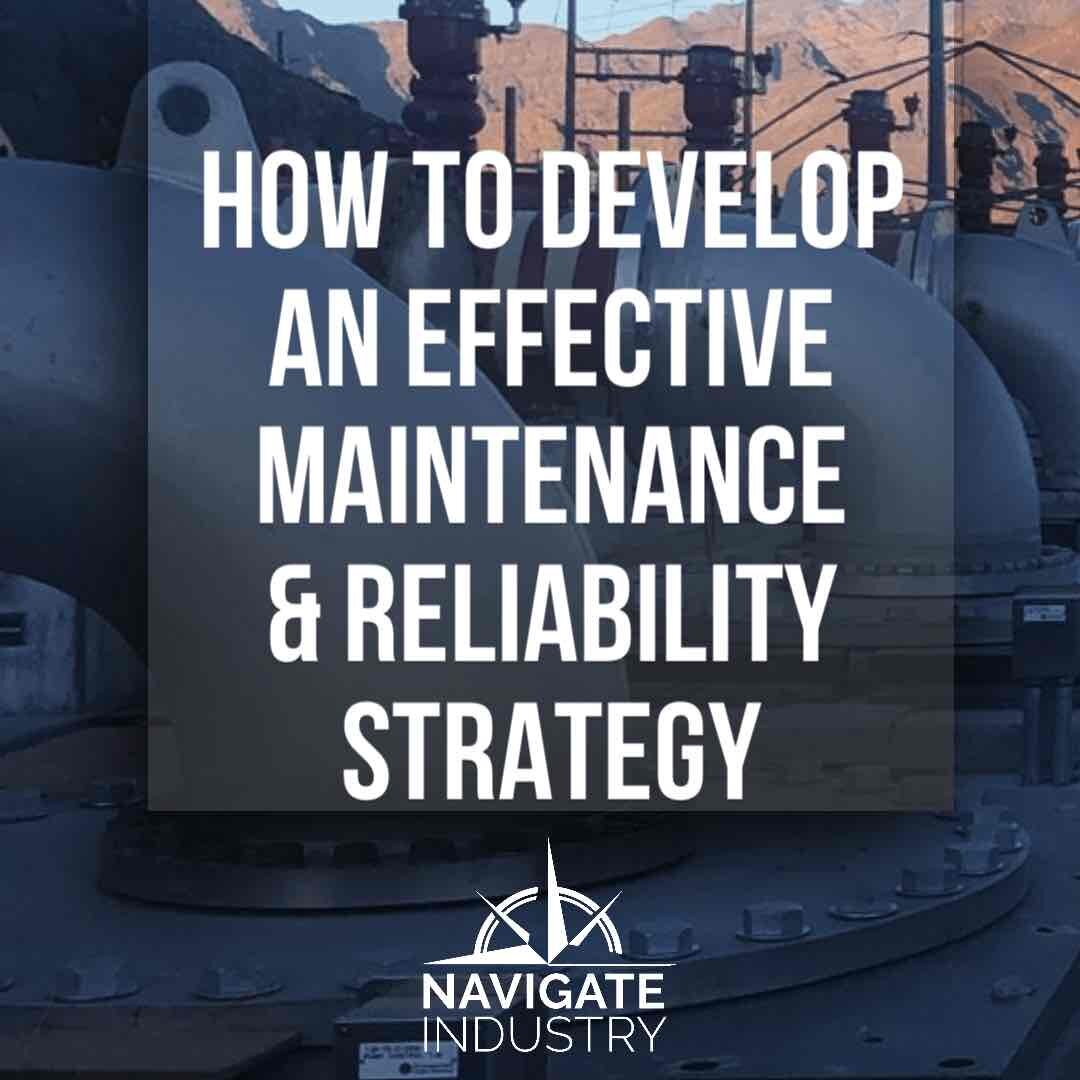
Growing up in Gwinnett County, Georgia, Clinton Davis was raised to believe that fixing things yourself is just a way of life. All of the men in his family were union plumbers and his father, Wayne, had a motto: “Never pay someone else to do something you can do yourself.”
The everyday practice of this philosophy provided Davis with hands-on experience in breaking down equipment, learning how it works from the inside out, paying attention to the details, and taking pride in putting it all back together and watching it work.
Davis remembers one single event that shaped his career path. He was 16, and the rear drum brakes on his 1978 Pontiac Grand Prix were worn out. He bought the parts, lifted the car, removed the wheels, drums, shoes, and hardware and then realized he didn’t know how to put it back together.
“I had not paid attention when I was taking it apart,” he said. “I was in a hurry and wasn’t patient.” He reluctantly asked his father for help.
His father explained to him that Lesson One in any project is the importance of paying attention to the details. “We walked back out to the car and my Dad told me he was only going to show me how to do this once. He put one side back together, and I had to watch him closely. Then he left me to figure out how to repair the other side. Many hours passed and when I was finished, he checked my work and gave me a few suggestions so I would learn.”
Six weeks later, Davis had to repair the front brakes. This time, he remembered the details. “I’ve been wide open ever since.”
Finding a Career Path in Maintenance and Reliability
Since that time, the now-43-year-old Davis remembers this experience with every project he undertakes. “I take my time when I break things down, even with projects and work requirements. I take the time to understand how all of the elements work together. This creates a better understanding and makes it easier to put it all back together.”
The experience was a turning point in shaping the direction of Davis’ career path. “It was just one of those moments in your life when everything falls into place,” he said. “I wanted to have the opportunity to work with my hands. And now I love to dive into the details. Most of our technicians are in these roles because they feel the same way. We find out a piece of equipment failed, we repair it, and then it is back to 100 percent. There is a lot of pride involved in what we do every day.”
Asset Reliability and Performance Management
Davis is currently the section manager of asset reliability and performance management for the Gwinnett County Department of Water Resources (GCDWR). Prior to this role, he worked for 13 years as a technician, analyst, and section manager. For the past several years he has been supporting a 3-to-5-year program designed to improve the maintenance and reliability at the GCDWR’s five facilities, which includes two water plants, three wastewater plants, and a pumps/tanks/boosters group.
Within the facility operations, there are approximately 222 employees. Davis’ section has a staff of 15 full-time professionals and two interns. “We support operations and maintenance from the customer perspective,” Davis said. “Our planners and schedulers are assigned to facilities and report there every day to plan and schedule for maintenance and operations. My staff is not all here in the central location. They are out in the facilities where they are needed.”
Getting the new program started was not easy.
In 2006, Davis was working as a trades technician on wastewater equipment in a centralized maintenance group. At that time, the wastewater and water plants were in separate divisions. The utility decided to implement a CMMS program at one of the facilities and Davis was selected for the implementation team, along with two other colleagues. They collected data, groomed data, coded data, and put it together to form the foundation for the new system. The team worked with some outside consultants for guidance and expertise. Eventually, his two colleagues moved on to other things and Davis was given the opportunity to run with it.
“I managed some maintenance-related projects and facilitated an RCM pilot project for one of our plants in the late 2000s,” Davis explained. “One of the drivers and takeaways from that project was realizing we needed a good system to make the most use of all the data so we would have the information we needed to make good decisions. Prior to that, everything was kind of paper-based and maintenance records were not as good as they should be.”
Reorganizing to Build Effective Maintenance and Reliability Strategy
The GCDWR underwent a complete reorganization in January 2014. The implementation team researched other utilities that had been positively affected by good maintenance and reliability programs. “The goal is to be a world-class utility and become the benchmark for others,” Davis said. “We did some peer exchanges with other utilities to learn how they are structured and organized. We studied the maintenance, reliability, and operational programs they have in place and how they communicated with their staff. These were all things we had struggled with organizationally in the past.”
With the reorganization, the utility moved from having water, wastewater, and pump/tanks/boosters as three separate entities to a homogenous and united family of facilities.
“Previously, all of these sections kind of functioned as little islands all unto themselves,” Davis said. “Everyone in each facility reported to the plant manager or plant superintendent. We had warehouse, maintenance, operations, housekeeping…everybody worked for the plant manager and they all did things a little differently. There was not a lot of sharing of resources from plant to plant. When large projects came up at one facility, it was difficult to get help from the other facilities.”
System Restructure with Maintenance and Reliability Strategy
Backed by strong leadership, support, and executive sponsorship, the entire system was restructured to break down the silos and effect positive changes in operations, maintenance, and reliability.
“We had some programs in place, but prior to the reorganization it was all kind of ad hoc,” Davis said. “We had a vision of what we wanted to be and what we wanted to do, but we had to figure out how to get there. We had to figure out what that road map would look like.”
The utility partnered with a local firm to dive into the weeds. In March 2014, they performed an asset-management best practices assessment. The firm spent two weeks on site, studied all of the data, interviewed technicians and operators, and got a feel for the morale and the culture.
“Beyond that, we did some staff engagement, which was something that had seldom happened in years past,” Davis said. “We brought in maintenance and operations coordinators and supervisors from all of our facilities for workshops to find out what was important to them. We made sure that senior management was not at the workshops. This gave them freedom to speak and be honest. We wanted to find out what they needed to be more effective in their roles.”
Implementing an Effective Maintenance and Reliability Strategy
From the assessment and the employee-engagement exercise, a 3-to-5-year road map was developed.
The assessment effort focused on seven key areas with 79 sub-elements. It included everything from effective planning and scheduling to having enough information in the job plans, to lubrication procedures, to communication.
“We can’t possibly implement everything on this road map individually or with a small group,” Davis said. “So we use a team-based approach, broken down into five focus areas.”
Leadership
Operations excellence
Predictive maintenance
Reliability engineering
Work management
Team members are operators, maintenance professionals, and warehouse staff. They work with sponsors and facilitators to get all of the elements implemented. Whether it is a change in the CMMS, exploring bringing in facilitators for certain projects, or critical equipment, the whole plan involves the team members so everyone will have an opportunity to shape the utility’s future.
“We have made some great progress in the past few years,” Davis said. “Planning and scheduling and warehouse staff have been through best practices implementations. Maintenance planning and scheduling was previously executed by our trades coordinators. We refocused and retrained the planners and schedulers, and have made enormous positive changes in quality and efficiency.”
Predictive Maintenance is Key to Reliability Strategy
For predictive maintenance, a team of internal technicians was formed. They are now in the middle of a 2-year project. Previously, contractors were used for this and there was no continuity. Oil sampling, precision alignment, and predictive maintenance are being performed internally by the predictive-maintenance team and maintainers at the facilities. Training and certification is offered to staff who perform these functions and more than 20% of maintenance technicians in infrared thermography and machinery lubrication have been certified.
“We trained our reliability engineers on root-cause analysis and did some cause mapping,” Davis said. “Our leadership team is focused on improving communication and helped train our supervisors and managers on meeting facilitation and public speaking.”
Applying Planning and Scheduling Improvements
Before the reorganization, the CMMS system generated work orders and the trades coordinator assigned them with no formal process. The utility personnel struggled to execute all of the required maintenance tasks.
“We were deferring about 10% of our routine maintenance because we just didn’t have the resources,” Davis said. “With the training of our planners and schedulers, we were able to get them focused on their core functions with weekly schedules and goals. They have used this to balance resources for maintenance. Now, if we have 400 hours available next week for maintenance at a facility, we are going to schedule 400 hours of work that is due to be completed. This keeps the maintenance staff focused on the schedule and getting the work executed.”
Prior to that initiative, the utility was only completing about 35,000 work orders/year, of which only 70% was work that had been planned and scheduled. As of December 2015, 89% of the work within facility operations is now formally planned and scheduled with an average of 59,000 work orders/year using the same-size staff. Completion times also dropped significantly from 3 hr./work order to just more than 90 min./ order across all proactive and reactive maintenance.
Davis credits this success to the effective implementation of maintenance planning and scheduling, warehouse best practices, training of staff, and using key tools and technology such as infrared thermography, vibration-analysis tools, condition assessment, and precision-alignment equipment. He added that using the CMMS every day to analyze information and find key areas for improvement is essential.
Emergency work orders are not formally planned, of course, but must be addressed immediately. The benchmark for planned and scheduled maintenance work orders is 95%. “It is ok if emergency or urgent work break the schedule,” Davis said. “But we must also take the time to investigate the failure and try to prevent it from happening again. My personal philosophy is that every failure is an opportunity to improve how we manage our assets. We are not perfect and, when something happens, we need to use it as an opportunity to understand what happened, why it happened, and learn from it.”
Mistakes to Avoid when Developing a Maintenance and Reliability Strategy
Challenges and mistakes along the way are simply a part of the journey. Davis said that the biggest mistake that can be made in implementing any new program is neglecting to engage the entire staff.
“We have some sharp people, but people are not always willing to tell you what they don’t like or if something is not working,” Davis stated. “If you are not engaging with them and working to get that information it may be a missed opportunity. I am a believer that negative feedback is sometimes the best information. Sometimes it’s a training opportunity or a need to improve a process. When we started out we talked about all the things we wanted to do from a technology standpoint and a best-practice standpoint. But without engaging the staff, we wouldn’t have made so much progress so quickly. We help them to understand how what they do every day relates to the big picture.”
Davis said the biggest challenge in implementing the new program was addressing the overall culture of the organization. “When we reorganized there was uncertainty. We moved some people around because we needed their knowledge and expertise in other areas. Most people don’t like change, and it is still a work in progress. We want people to enjoy their work and share their opinions and concerns.”
Building the right team is also essential, Davis said. “We look for people who have aptitude and ability, and this is equally and sometimes more important than the functional ability to do the job. We are always looking for team players.”
A Focus on Continuous Improvement
With continuous improvement the never-ending goal, the work is never done. The checklist comes from the details and the daily progress that contributes to the overall big picture.
Davis has learned that when assembling and implementing a program such as this, a focus on “everything” may get you nowhere. “It’s never going to be finished. You have to focus on getting the staff’s skills up to speed, mentoring, bringing in some experts, and start a little smaller. You must pare it down to what you need in the immediate future, and what you can successfully implement and sustain. Then build upon that.”
The GCDWR’s road map is laid out sequentially. “So, if I float off the planet tomorrow someone can come in and make sense of it,” Davis stated. “And, like my father taught me, it’s always about paying attention to the details. Through this 3-to-5-year program, we came out of the gate after the first assessment at 47% out of 100, give or take. We just had our 2015 assessment and we are up to 63%. These are the opportunities I enjoy because it visualizes all that progress of all those little details. And it’s easily shared with other people. We can all see the progress.”
From the age of 16, Clinton Davis knew he wanted to work with his hands, repairing and building things. So whether it’s rebuilding the ’78 Pontiac or helping to implement an entire maintenance and reliability best-practice program for a huge utility, he uses these skills and lessons learned to this day.
Michelle Segrest is President of Navigate Content, Inc., a full-service content creation firm. She has been a journalist for more than three decades and specializes in covering the people and processes that make a difference in the industrial processing industries. Contact her at michelle@navigatecontent.com
If you like this article about developing an effective Maintenance and Reliability Strategy, please PIN IT!
This page contains affiliate links. If you click on the product links and make a purchase, it allows me to make a small commission at no extra cost to you! Thank you for your support and I hope you find value in this content!