Preventive Maintenance Helps Eliminate Deferred Maintenance
/Michael Flint drives a preventive maintenance strategy at Brown University to help direct wasted man-hours toward reducing a large and growing deferred maintenance backlog.
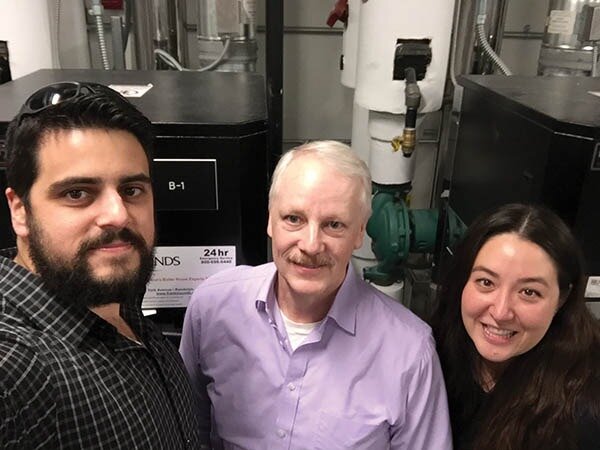
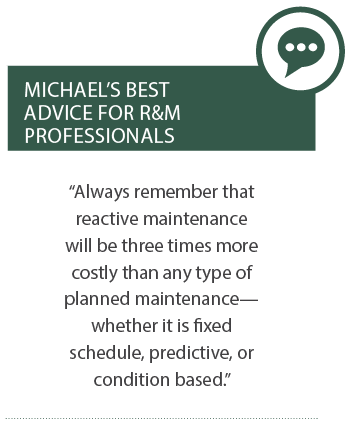
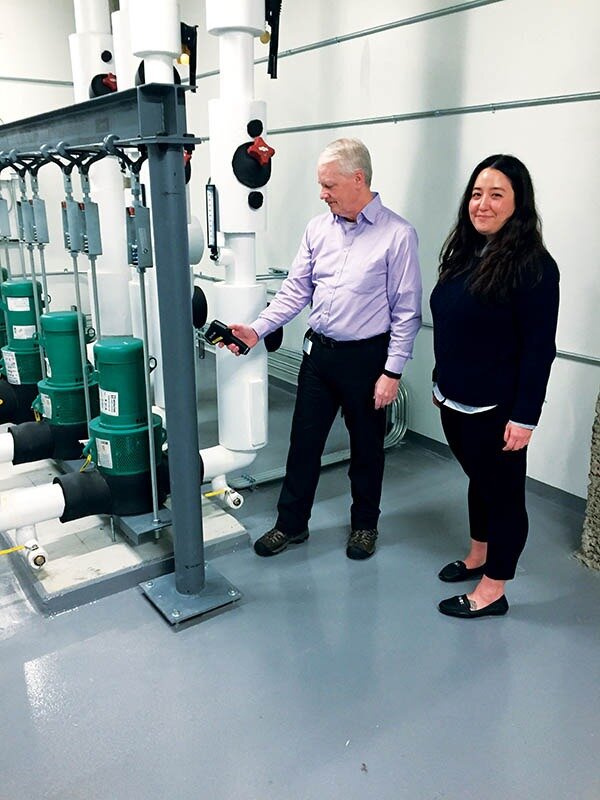
By Michelle Segrest, Navigate Content, Inc. - Reporting for Efficient PlantMagazine
Growing up on a dairy farm in western New York state, Michael Flint learned early the value of proper maintenance and the safe operation of equipment. He also learned the importance of properly caring for the livestock.
Though he didn’t know it at the time, this experience prepared him for his current challenge—driving a seven-year program at Brown University designed to redirect 57,000 work-process man-hours used to maintain 226 buildings covering 6.34-million sq. ft. at the Providence, RI campus.
“On the dairy farm, I learned the concepts of maintenance and reliability,” said Flint, the preventive maintenance manager for facilities management. “I learned that most equipment required lubrication and visual checks to make sure everything was operational before we went out in a field to perform harvesting activity or use of that equipment. The animals also had a certain care schedule, which involved feeding and the cleaning of their environments.”
Flint uses this base and his previous experience managing maintenance at a central-station power plant to understand how to best provide building system preventive maintenance (PM) services at Brown. He leads a team that includes two planner/schedulers, Mike Lopes and Angela Cunningham. They support PM work planning for three maintenance managers, six maintenance supervisors, a maintenance staff of more than 100 technicians, and two service-contract managers. Flint and his team drive the strategic preventive-maintenance and reliability efforts.
“Managing a campus like this is certainly a challenge,” Flint said. “Rarely do the same issues crop up every day. We have large commercial office buildings, large laboratory and animal-care spaces, and many historical houses. All of them have their own specific needs and challenges.”
Strategic planning and scheduling is crucial to making it all work, Flint said. The team uses a hybrid zone-and-trade maintenance strategy rather than a geography-based model. The trades are HVAC, electrical, plumbing, building controls, and structural specialties.
“It’s an intricate matrix,” Flint explained. “A lot of the planning is done by areas of expertise and building criticality. We have a hard time thinking that we are big enough to organize by geography or zones by themselves. Even though we have a lot of buildings to maintain, the campus is fairly compact, so we opted for the hybrid model.”
Implementing a New Preventive Maintenance Strategy
Flint initially entered the reliability and maintenance field in the 1990s, when he spent six years as a supervisor at that electric power plant in western New York. At the time, plant managers were trying to address increasing maintenance budget pressures and Flint led a program to implement a new PM strategy.
“I took on the role in the organization to develop a revised maintenance strategy, which would lead to reduction in unplanned equipment down times and limit overall maintenance budgets,” he said. “During this time I developed a maintenance and reliability philosophy that the most important thing is to focus on how to better plan and execute all maintenance activities that will have the least effect on operations while keeping the equipment operating efficiently and reliably for the long term.”
Flint began then to develop some maintenance and reliability best practices that he continues to apply daily. It starts with strategic planning and then targets PM and long-term reliability.
“I tend to be a strong maintenance planner, team builder, and change-management leader,” he said. “It’s important to focus on common goals. Through the maintenance team pulled together here at Brown, we are developing the desired best-in-class maintenance which is extending equipment life and reducing interruptions on all building services.”
Most of the university’s maintenance happens on a fixed schedule. For example, the air-conditioning systems get routine filter changes, lubrication, and control checks. The buildings themselves are prioritized into seven categories—research, academic, student housing, administration and support, athletics, student activities, and auxiliary housing. The most critical buildings receive more frequent and focused maintenance activities.
Building an Aggressive Preventive Maintenance Program
When Flint was hired almost four years ago, the university had already worked to develop a PM strategy that included a way to help fund the PM activities. Brown staff used Lean techniques to identify waste in the maintenance work processes that could be redirected into the needed PM activities. More than 57,000 man-hours of waste were found, which is now being recovered and redirected as part of the seven-year strategy implementation.
“Our preventive strategy is really an umbrella that includes any planned maintenance activity,” he said. “You can use technology for predictive things like condition-based maintenance. The idea is that [the university], through support of a consultant, identified that we had a significant deferred-maintenance (DM) backlog of $470 million that was going to continue to grow at $48 million each year. The best way to help address this backlog was to strengthen the preventive-maintenance program. Through the focus on preventive maintenance and other actions by Facilities Management, we have limited the increase in deferred maintenance to just $7 million total over the past four years.”
“We are in the fifth year of the seven-year program to strengthen the preventive-maintenance program,” Flint said. “The formula was that we simply had too much maintenance and not enough hours, and this resulted in higher costs for things like overtime or additional and emergency contracted services. We also have equipment that is getting older and requires more maintenance.”
After the initial focus on the effective application of fixed-schedule maintenance, the goal became to develop a strategy to help deliver a change in the maintenance-staff culture. The next step involved applying predictive/condition technologies that include vibration data collection and analysis on all critical rotating equipment and infrared monitoring of major electrical-distribution equipment. In addition, runtime-based maintenance actions are being initiated by the building-automation system with the direct creation of the necessary maintenance work orders.
Measuring Results of a Preventive Maintenance Strategy
One of the key performance indicators for the program was measuring planned versus reactive maintenance activities. When the program began, the campus operated with only 25% planned maintenance. Five years later, 68% of the maintenance is planned.
This was accomplished through a redirection effort that incorporated a variety of Lean manufacturing techniques. Processes that were wasting critical man-hours were identified, providing a clear path for finding reasonable improvements. Some of these improvements were identified prior to Flint’s arrival thanks to a broad team of front-line staff, management staff, and participants from some of the larger campus departments.
Also, converting to a PM mindset was crucial in the efforts, but this required a steady change in the overall culture.
“We focused on making many small changes rather than big ones,” Flint said. “Soon, change itself became part of the culture and therefore made it easier to implement the major changes. Change, in general, has become something that is just expected in our culture. Until someone tells you that you have to begin to do things differently, you can’t understand the impact this will have on you. We made sure that all the changes didn’t happen at once, but they happened regularly—so the idea of change was never a surprise.”
For example, the team switched from using a desktop PC to using a mobile maintenance-work-order system. Each technician now carries a tablet in his/her tool case and documents all work history and spare-parts needs remotely. This helps eliminate wasted time that has been redirected into other PM activities.
Finding Inspiration to Build a Best-in-Class Facility Team
Flint relies on sage advice from Theodore Roosevelt: “Far and away, the best prize that life offers is the chance to work hard at work worth doing.”
“We have a serious goal of working toward being a best-in-class facility team,” Flint said. “In my work experience, I’ve been involved with organizations that try to think that way and often they compare themselves with other companies to try to capture and implement what is working for others. In my opinion, this doesn’t make you best in class—it might make you almost as good in class as the ones you’re trying to duplicate. So you really have to do more than that. You have to think for yourselves along with taking advice and using the best practices that you see others doing.”
And how do you know when you get there?
“In my mind you never get there,” Flint said. “There should always be something else that you can do better.”
Flint’s Top 5 Tips for Maintenance and Reliability Professionals
Plan for everything, including failures.
Measure for success—correct to improve.
Communicate, communicate, communicate.
Review new installations for safe maintainability.
Feedback from the staff performing all maintenance activities is a must.
Michelle Segrest is President of Navigate Content, Inc., a full-service content creation firm. She has been a journalist for more than three decades and specializes in covering the people and processes that make a difference in the industrial processing industries. Contact her at michelle@navigatecontent.com