Precise Calculation Leads to High Performance Engineered Equipment
/Johan Meijer has spent the past four decades solving engineering problems related to pumping system design—working closely with valves, pumps, and hoses. His experience and knowledge became so deep he developed a powerful and strategic calculation program for high pressure peristaltic pumps that is provided free to end users.
By Michelle Segrest, Navigate Content, Inc. - Reporting for Valve World, Pump Engineer, and Hose+Coupling World
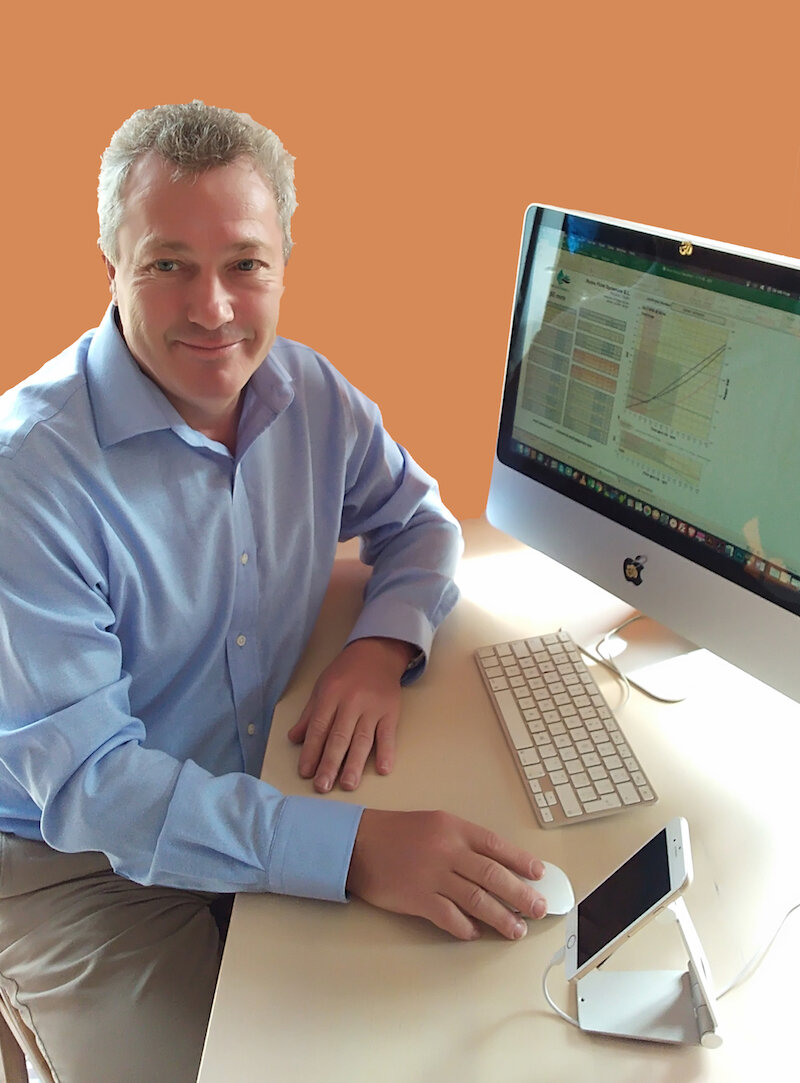
For Johan Meijer, pumps and valves are close to home. “Valves and pumps are more than just work for me,” he said. “They are my hobby.” At his home in Andalusia, Spain, he and his wife have five pumps for the water supply, all controlled with a PLC that runs on solar energy, and his swimming pool has a filtration system with pumps and many valves, as well.
Originally from the Netherlands, Meijer spent his early engineering years working in the United States. From ages 24 until 37, he worked with major companies in the food & beverage and specialty chemicals industries with a major engineering company in Atlanta, GA. Most of this experience included hands-on learning.
Seven years ago, Meijer and his wife decided to make a lifestyle change and moved to southern Spain, where he started his own business. The business began with wastewater treatment consultancy, working on polymer dosing systems, and foamed concrete systems for the pre-fab construction industry. In addition to all these activities Meijer continued to develop a program for calculating the most effective pump sizes of high pressure peristaltic pumping systems.
After his 14 years working in the U.S., Meijer returned to the Netherlands, working as sales manager for a major peristaltic pump manufacturer. He began to build expertise with peristaltic pumps including valves, hoses, and all other items that make up the entire system.
“I was first hired as a senior designer, assisting with process background as a certified operator in the chemical industry but also as a qualified safety engineer, helping the design teams,” he said. “At that time, I was one of the only engineers at my company who was good with computers. That helped me a lot because the old school engineers were just using calculators and not using spreadsheets like Excel and doing the work on a PC. This was early late 1980s through the early ‘90s when the Internet was just being introduced. I was able to work with all the different types of engineers helping them with their calculations. That’s where I got involved with pump selection and calculating tank capacity, pressure relief valves—actually everything that has to do with process technology.”
During this time, one of his major duties as a process engineer was sizing pumps and related pipe sizes, valves, filters, etc.
“When you are in charge of sizing a pump, all the piping, inlet. and discharge aspects are part of that,” Meijer said. “You must look at the whole system. Everything is part of the selection. The liquid needs to go in the pump and come back out with enough volume coming back out of the pipe. For example; if you have a centrifugal pump with just enough pressure to pump the liquid up the hill, but not enough to pump it over the hill, then it just sits there in the pipe and doesn’t do anything.”
In this case, the pump size as well as pressure drops must be considered.
“Then you have to think about the valves, and all other items connected to the system,” he continued. “When you are thinking about maintenance, if you have to shut down a pump, you need valves to isolate the pump. Valves have their own dynamics—flow coming in and flow going out—and there is a certain resistance. All this calculates up. The fluids we transfer are not only just water. You should consider all the different effects of the fluid—like density, viscosity, and temperature. This affects the friction in the pipeline and the energy that is needed. You must consider many things in the system. You need to know about the pumps, valves, and all other items placed inline equally in order to engineer a good system.”
Correct Pump Selection Affects the Entire System
Meijer has completed a generic peristaltic pump selection program designed to select and troubleshoot high-pressure peristaltic pumps for plant engineers and operators. The program includes his lifetime of knowledge and experience.
“A few years ago I made some notes for myself so that I wouldn’t forget all the knowledge I had gained during all those years working with pumps,” he said. “I put it all in a spreadsheet, then decided to make a small calculation program that included everything I know about properly selecting a high pressure peristaltic pump. I then combined all this information to develop a very powerful selection program that includes a life-time of experience.”
Analyzing & Solving Problems with Rotating Equipment
Meijer’s specialty is analyzing specific problems with equipment and helping to provide solutions.
“For example, a plant may have a pump with a hose that has a hose-life of only 500 hours,” he explained. “If they run the pump 40 hours per week, they must change the hose of the pump every three months. This becomes expensive, especially if they have five or six of these pumps. So I will help them figure out how to solve this problem. I also handle analysis of failed equipment. Sometimes the failing of the hose is not caused by the pump selection but be- cause of the manufacturing of the hose. Perhaps it’s not the quality that they originally thought. How do you know if the hose is faulty? You only know after running the pump for a week or so. I give them pointers on where to check and how to check it using my technical expertise. This is another way I help the end users.”
Meijer described another problem he helped to solve, this one from a wastewater treatment plant in California.
“They had about 20 large peristaltic pumps with 100mm hoses with very long inlet lines,” he said. “When I was invited over there for solving the short peristaltic pump hose life problems, I noticed the inlet lines were very long and the systems had very high pulsation everywhere. The pulsation dampeners that were installed were not working as they should, and some of the pumps did not have pulsation dampeners at all. At this point I began calculating with as built data. After supplying the results and my recommendations, this plant implemented the changes and ex- tended the hose life with an average of three times—a savings of approximately $65,000 USD per year.
Meijer’s program allows end users to insert data such as inlet and inlet dis- charge piping with multiple branches, together with all the fluid details, viscosity, density, temperature, etc., and at the end, it provides a curve that indicates exactly the Best Efficiency Point and operating range for the pump to be running, including the pulsation pressure losses for the inlet and discharge side of the pump.
“You must look at the whole system and calculate the pump size and see where the pump is running,” he explained. “Knowing pressure conditions on the inlet side of the pump is extremely important. Most people think pump performance is all about discharge. For nearly all pumps, the inlet is the most sensitive part of the pump, and this needs to be looked at properly because the vacuum is a very small but strong number. If you have one bar of vacuum it is absolute, and this is really strong. Whereas a discharge pressure can exceed 600 bars or higher. If you have half a bar of vacuum on the pump that is pulling on your seal enormously your seal, your seal will be working in two directions (in and out). If the pump is in a clean room you don’t have to worry about getting dirt into the seal.
“But if the pump is in an unforgiving area and you have vacuum on the seal, it will pull dirt into the seal and cause the seal to start failing from the outside in. Even with double mechanical seals, there is still a risk on the suction side. The same is true with the hoses. On the inlet of the pump, the suction side is pulling enormously on the inner layer. Together with the pulsation effect, you start getting a ripping effect—pressure on, pressure off. This can cause delamination (when the reinforcement lets loose from the rubber). When this happens your capacity drops because the hose is not pulling back to it’s original shape, which causes a volume decrease. Your inlet pressure will also change because the pulsation de- pends on the volume you are pumping.
“The pulsation (also called acceleration losses) is caused by the fast repeating starts and stops of the fluid flow. The Pulsation creates additional pressure to overcome. You can see these pulsation losses on the curve. The pulsation changes based on pump speed, fluid flow, length and diameter of the piping, density of the fluid. Often the pulsation can be solved with different types of pulsations dampeners. Pulsation dampeners are actually flow/volume harmonizers, and with a constant flow/volume you will have a constant pressure – no pulsation.
“Adding Pressure Sensors at the inlet and outlet, and you can add an alarm to indicate when the pulse is getting lower to indicate you have a failure. Most common failures on the peristaltic hose are on the suction side, these failures start on the inside the hose and travels through the reinforcement layers in the middle of the hose, then builds up and blows out of the outer layer of the hose on the discharge side into the pump housing. It is believed by many users that it is a pump discharge problem, and they spent usually lots of time trying to solve this at the wrong side of the pump.”
Peristaltic pumps have been around for more than 60 years, Meijer said. And often with copies of similar manufacturers, together with the performance curves. Meijer’s program creates a performance curve that includes the actual liquid properties and pulsation.
“During my employment with a leading peristaltic pump manufacturer, I was able to study the behavior of pulsation in great detail,” he said.
“Removing pulsation out of any pump that has pulsation reduces the energy needed quite a bit. Surprisingly, after all these years of being told that the pumps had a linear curve, I saw with my program this was not the case. The result has been amazing. I got a parabolic curve. With this program, I am hoping to reach out to as many as possible peristaltic pump end users to re-evaluate their installation and find the best operating parameters and pump size to reduce the cost of replacement hoses and downtime.
“When pulsation is not desired, then it will safe lots of energy, spare part, and costly downtime of the process. This is not only for peristaltic pumps but for all pumps that have pulsation as a side effect of its pumping behavior.
Proper Preventive Maintenance for Pumps & Valves
Meijer said that most problems with pumps and valves exist because the documentation for selection does not exist at the end users location or is not being used in reference when ordering spare parts. Also, the knowledge and awareness of maintenance personnel can be improved with specialized training for the high cost maintenance equipment, such as high pressure peristaltic pumps.
“It is necessary to evaluate the failure of a pump or a valve with a qualified engineer if the cause of failure is not obvious,” he said. “This might prevent the pump or valve from having the next similar failure.”
Most common failures with pumps in general are the drive shaft seals, he said, while for valves the most common failure are the valve shaft seals and valve seats. Most of these can be solved with a good preventive maintenance program, Meijer advised.
“For all valves and rotating equipment, it is necessary to have regular inspections for dripping leaks and mechanical movement,” he said. “Naturally this can be done the best when the equipment is kept dry and clean.”
Sharing Engineering Experience & Expertise to End Users
Meijer offers more expert advice for young end users.
“Young end users for pumps, valves and other process equipment can quickly become knowledgeable when they spent time watching YouTube and using the Internet search engine to ask questions and read about info that has been posted,” he said. “But it is also extremely beneficial if they can get hands-on training classes from engineers with lots of years of experience. It is very important to get educated in safety procedures for the process industry. One of my preferred ways is asking HAZOP questions together with ‘what if’ analysis.”
Meijer emphasized that the more experienced engineers have much to offer to the next generation of engineers.
“It is interesting that with all pumps you have must have valves,” he said. “Valves must be selected with the same care as the pumps. The material of construction is important for the valve body, but especially for all the parts that are in contact with the fluid to be transferred. By knowing that valves need to be operated, the location in the system is important and also the safety is something a designer or an installation company should not take with a grain of salt.”
Meijer said that some key words to con- sider when looking at valves for a system should include:
Material of Construction (for chemical compatibility)
Pressure Rating
Vacuum Rating
Temperature Rating
Flow Requirement
Flow Direction
Movement (Open Close or Flow Regulating)
Environmental Factors (interior/exterior)
Fluid Characteristics (Fluid or gas, solids, viscosity, density, abrasiveness, and scaling)
Safety—Apply a HAZOP to the system, but also on each valve.
Meijer’s program is available to students, engineering companies, and end users who are not commercially involved selling pumps. Distribution and Engineering companies who are selling or specifying high pressure peristaltic pumps can use this powerful program for a small licensing fee. You may request your copy by email – hosepump.sizing@gmail.com.
Michelle Segrest is President of Navigate Content, Inc., a full-service content creation firm. She has been a journalist for more than three decades and specializes in covering the people and processes that make a difference in the industrial processing industries. Contact her at michelle@navigatecontent.com