Reliable Maintenance at the Y-12 National Security Complex Mini City
/A focus on PM optimization, culture change, sustainable processes, and employee empowerment drives reliability efforts at the Y-12 National Security Complex mini city.
By Michelle Segrest, Navigate Content - Reporting for Maintenance Technology Magazine
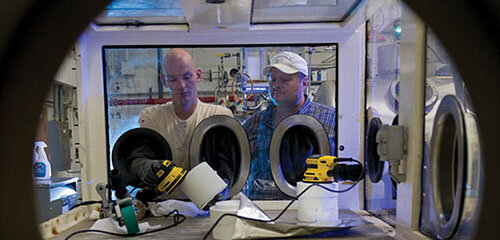
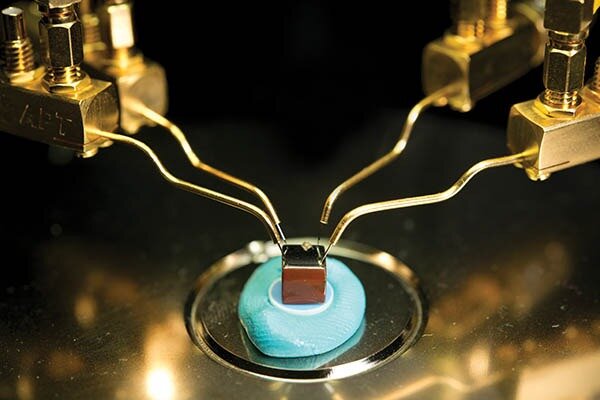
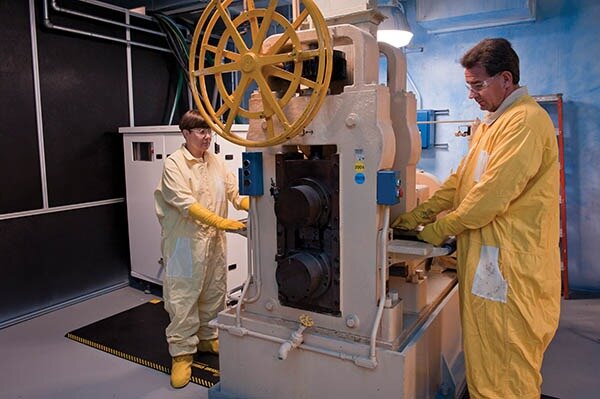
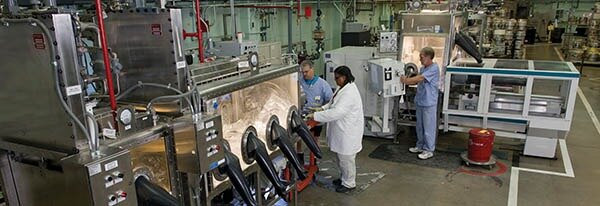
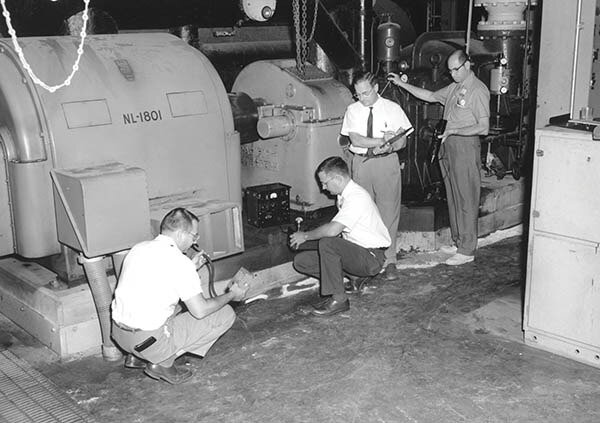
Spanning 2.5 miles between its east and west boundaries, the 74-yr.-old Y-12 National Security Complex is a “mini city” inside the city of Oak Ridge, Tennessee. Within its secure borders are 379 buildings of manufacturing, production, laboratory, support, and research and development areas managed by Consolidated Nuclear Security LLC (CNS) under contract for the National Nuclear Security Administration (NNSA).
Y-12 also includes its own armed security force, fire department, steam plant, medical facility, cafeteria, and electrical-distribution center, all of which accommodate the nearly 8,000 people who work within the “city” borders each day.
Led by director of enterprise reliability and maintainability Joe Boudreaux, a 45-member reliability team is responsible for the proactive maintenance strategies of the buildings on the 811-acre campus. Deep into the second of a five-year reliability-improvement program, the team has built a firm foundation and is now strategically navigating its road map with the ultimate destination of establishing a sustainable, proactive maintenance program.
“Within the building site there are mini-plants within the city,” reliability and maintainability manager Paul Durko explained. “And within each of those mini-plants, certain processes, systems, and cultures that exist. Our goal is to secure a sustainable system of processes that work across the board, promoting an increase in overall reliability for this aging site. But it also has to be a system that will translate to a new facility—a $6.5 billion uranium processing facility (UPF) that will be built and in operation by 2025.”
Y-12 HISTORY - Strengthening the U.S. National Security
Since 1943, Y-12 has played a key role in strengthening the United States’ national security and reducing the global threat from weapons of mass destruction.
The Y-12 National Security Complex is one of eight sites in NNSA’s Nuclear Security Enterprise (NSE). Y-12’s unique emphasis is in the processing and storage of uranium and the development of technologies that are associated with those activities. CNS also manages the 18,000-acre Pantex plant in Amarillo, Texas, which is the primary U.S. nuclear weapons assembly, dismantlement, and maintenance facility. A majority of the weapons-related operations at Pantex are conducted on 2,000 acres of the site.
Constructed as part of the World War II Manhattan Project, Y-12 provided the enriched uranium for Little Boy, the atomic bomb dropped on Hiroshima, Japan to help the U.S. and its allies end a war that had taken 63 million lives worldwide. Afterward, Y-12 provided lithium-separation functions and key components for thermonuclear weapons. Y-12’s expertise in machining, handling, and protecting radiological materials has made the Oak Ridge site central to the nation’s nuclear security.
Y-12 has developed state-of-the-art capabilities in three core areas: nuclear technology and materials, security and consequence management, and manufacturing and technical services. Y-12 lends its specialized expertise to other federal agencies, such as the U.S. Departments of Defense and Homeland Security, state governments, and private-sector companies.
Projects at Y-12 include providing protective equipment to soldiers in combat, training National Guard units for radiological emergencies, and creating machining platforms that improve production and efficiency.
More than 9,200 Tennessee citizens work at Y-12, including federal and contractor staff.
“Our primary responsibility is to make sure the nuclear weapon is reliable,” Boudreaux said. “We do all of the testing and checking to make sure that if there is ever a need to use a nuclear weapon, that that weapon will work. The whole goal of the plant is global threat reduction, and when you think about all of the components that go into that, there are a lot of different things that have to be done here. So it’s not just a single process.”
Pursuing World-Class Manufacturing Reliability
With a commitment to reliability and with corporate support, Y-12 commissioned the University of Tennessee’s Reliability and Maintainability Center (UTRMC) to perform benchmark assessments. The next step was building pillars for the foundation of an overall reliability program. This included plans for an improved culture, PM optimization, training and education, full utilization of technology and software, increased ratio of proactive to reactive maintenance, continuous-improvement plans, scheduling improvements, and employee retention.
The UTRMC provided a subject-matter-expert (SME) analysis of the current state of the Integrated Work Control (IWC) and Maintenance Execution processes. The evaluation consisted of site visits and evaluations of the essential elements, including:
synchronization of production, engineering, and maintenance reliability
improvement efforts
targeted opportunities for improvement
plant employee training opportunities
methodology for transitioning plant personnel from tactical (reactive) maintenance
methodologies to a strategic posture
development of a reliability-based plant culture.
“We talk a lot about the ratios between how many corrective maintenance jobs to do and how many things we do that are proactive,” Boudreaux said. “When you look at Y-12, you can’t just look at that globally. You have to look at the individual component. If you would take a step back, we are a very reactive maintenance organization. So, what we have done over the past few years is to try to turn that from a very reactive program into a proactive program. A lot of things we are seeing are all these unplanned failures. And honestly, maintenance has become very, very good at firefighting. But it is very, very expensive to do that.”
The pursuit of world-class reliability has been a slow but fruitful process.
“The way that our program was set up, we feel like we have turned the big battleship,” Boudreaux said. “It’s a big ship and requires a slow move to get it to turn that corner. One way to be more cost effective is to decrease the amount of corrective work that we do. How do we do that? We reinvest in the plant. We get new equipment, and we maintain it the way we are supposed to, but we also look at the equipment that we have and ask what we can do to increase the reliability of those assets. We know that doing preventive maintenance is safer, but we can also save costs this way.”
One huge early success has been optimization of the PM program.
“We have increased the interaction of our crafts with the development of our packages,” Boudreaux explained. “By going through our PM optimization (PMO) process, we now have more thorough documentation and better estimates of the time and resources required for each PM. We can now identify the costs and the benefits.”
The next step is communication. “It hasn’t been a difficult sale, because very few people would drive a car for two years and never change the oil,” Boudreaux explained. “A robust PM program just makes good sense. And we now have documentation that clearly lays out the tenets of reliability. We now have a road map that explains what we have done and what we should be doing over the next few years. Part of the plan is to ensure this plan is communicated to everyone in the plant.”
Communication helps to provide influence within the organization.
“Paul’s [Durko] responsibility is to influence the maintenance craft, for example,” Boudreaux said. “He works with the maintenance manager and his maintenance-execution team. He is arranging for additional training to help improve skills and capacity. With great communication and influence, we can produce a better-quality product for our customer. The road map shows how everything fits together for the future.”
One of Y-12’s core missions—maintaining the safety, security, and effectiveness of the U.S. nuclear weapons stockpile—translates into the overall reliability mission.
“If you want to think of similarities, you can look at the production goals for our different systems,” Durko said. “We must break down the different processes, look at the availability requirements for that equipment, and understand what we are doing to ensure the equipment can meet those production goals. What we did well for many years is that when it breaks, we are going to fix it. With an aging facility and with this aging workforce, the challenge now becomes how to do it cheaper. How are we effectively managing our assets? What appropriate programs do we have in place to ensure that that equipment will operate when it is supposed to operate? This is how we integrate the idea of reliability across the site.”
With a distinct plan and road map to get there, all the pieces begin to come together.
“We understand that each milestone is just a piece and not overall reliability,” Durko said. “We now consider all of the tools in our tool belt—RCM analysis, PdM technologies, SAP integration, procedural requirements, etc. Bringing all the tools together to make the systems cost effective and also ensure the safety of our people and equipment are the ultimate ingredients that will get us to overall reliability.”
Proactive Maintenance Strategies
The focus in the first year was building a robust proactive maintenance program, Durko said. “Our past strategies and mission focus have caused us to become superb at finding ways to keep our failing systems running. We have begun shifting our mindset.”
The Y-12 site averages 2,750 completed maintenance orders each month, with an average of 99% utility availability, and has set a goal of 40% reduction in planning time.
“We are now averaging 64% reduction in planning time,” Durko said. “We are also proud that we recently reached 50,000 safe work hours with the PMO program. A bonus result is a 20% reduction in execution time. That is easy to sell to customers. Any time you say optimization, you automatically think of cutbacks and loss of jobs.” He added that because the plant had been in a reactive mode, they have been able to talk about the amount of reactive versus proactive work and actually improve the PM program.
The proactive maintenance strategy includes condition-based maintenance using ultrasound and vibration analysis tools, Durko said. “Also, document control is a key tool. We are dependent on what all that data is telling us to be able to make our decisions.”
With the proactive strategy taking shape, the next step is standardization, Durko said. “Having a repeatable process is key. We have standardized the format in a way that the crafts can better use—they actually helped us develop the format, so now it’s about execution. Next, we want to find a way to better rely on our predictive methodologies and leverage our technology. Hopefully, the data will tell us what is the next step. Meanwhile, we are refining our lubrication program with ultrasound and honing our precision-maintenance skills.”
None of the improvements made thus far would be possible without the interface and support of the technician work force.
Increasing Condition-Based Maintenance
The next goal is to increase condition-based maintenance work by 15% in the next fiscal year.
“I don’t think our road ever ends,” Boudreaux said. “You can always find a way to be even more reliable. But if we have that foundation, and we build off of that, then every time we bring something in, we can evaluate it against what we are trying to achieve with the program and see whether or not it has value. Having a firm foundation allows us to do that. The exciting part is to have some programs in place and begin to see the data that tell us it’s working.”
Y-12 BY THE NUMBERS
Y-12 today:
• 811 acres, including 150 that are high security
• 7.3 million sq. ft. of laboratory, machining, dismantlement, research and development, and office areas
• 343 buildings, 13 mission-critical facilities
• 48% of all Y-12 facilities are more than 60 years old
• ~9,300 personnel at Y-12
• ~4,700 CNS employees; remainder are subcontractor and federal employees
• Deferred maintenance of $354 million• Contracts with more than 770 small businesses, totaling $177 million in FY 2016.
Y-12 site includes:
• 550,000-sq.-ft. on-site leased facilities (Jack Case and New Hope Centers)
• 24 mi. of paved roads
• 10 mi. of overhead steam lines
• 3 mi. of natural-gas-distribution lines
• >55 mi. of aerial electrical-distribution lines
• 10 mi. of underground electrical-distribution lines
• 19 mi. of main water piping
• 50 mi. of storm drain lines
• 15 cooling towers.
Original version published in Maintenance Technology, August. 2017.
Updated October 2019.
UPDATE: As of October 2019, the Y-12 National Security Complex is a 76-year-old plant with around 5,800 employees and more than 10,000 people on site every day.
Michelle Segrest is President of Navigate Content, Inc., a full-service content creation firm. She has been a journalist for more than three decades and specializes in covering the people and processes that make a difference in the industrial processing industries. Contact her at michelle@navigatecontent.com