Identifying and Solving Technical Issues During Commissioning
/As a senior inside sales engineer, Kirill Zimin is in charge of sizing pumps and selecting and acquiring quotes of its accessories. This requires meeting with customers as a technical expert. Working closely with the sales force at Ruhrpumpen Global, his team must accurately transfer orders to the manufacturing business unit in the oil and gas, power, chemical, metallurgy, and water industries.
By Michelle Segrest, Navigate Content, Inc. — Reporting for ValveWorld, ValveWorld Americas and Pump Engineer
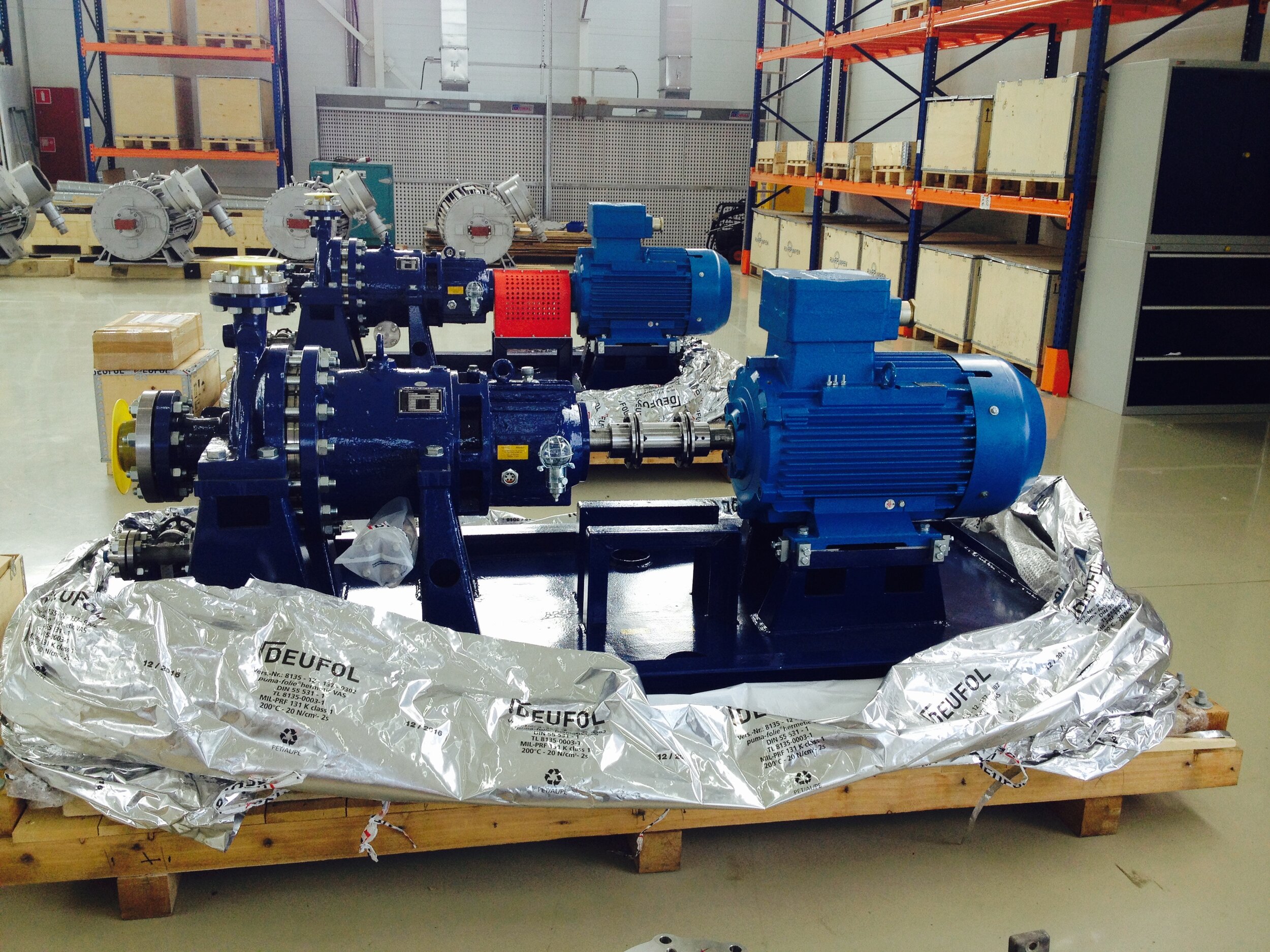
Focusing mostly on the oil and gas market, Kirill Zimin has deep knowledge and experience. Project-to-project, he must meet customer needs while also resolving new design issues.
“It attracts me to update information from different sources like design engineers’ communities, pump magazines, international reports, and books,” he said. “My experience starts from university classes where I took lessons in hydraulics with process and apparatus, focusing on theory. At the end of the bachelor program I had to search for work.”
He said he is grateful for that period of time and for the conditions. Without many options for engineering or managing roles, he got core experience using a combination of physical activities like collecting oil products, probes, painting structures, repairing valves and heat exchangers, and of course, learning more in his university studies.
“During this period, I spent less time on the investigation of industrial equipment and environment,” he said. “That’s the cost of sitting in two chairs. I passed my exams on sedimentation in electric dehydrators. Then I moved on to working for my master’s degree. This is where I started to learn equipment like valves and pumps. I took part in the repair of this equipment. The pumps were manly OH2, BB1 pump types as per designation to API 610. I mostly worked with gate and regulating wedge-type valves. Regulating valves are pneumatically governed.”
After earning his master’s he became a foreman in the subdivision of storage and loading of oil products.
“I was in charge of repairing pumps, valves, and other equipment,” he said. “In my new role of leading mechanical engineer, I was in charge of the technical extension of existing facilities in the subdivision. Equipment types varied, but there was now a new type of pumps and valves for further learning. After a few years I was invited to a group of the commissioning of a new facility. It was luck. It was the most efficient time for working with a team and learning new complex equipment.”
In this role, he worked with screw and reciprocating pumps—also BB1, BB2, BB5, OH1, OH2, VS1, VS4, VS6 types as per designation to API 610. In addition to wedge type valves, there were ball types with an external quench system, and sliding gate valves hydraulically operated for coke drum chambers and relief valves.
“After a few years in this role, I gained a lot of experience and skills,” he said. “This lead to an invitation to commission a hydrotreatment unit as a leading technical expert. This technological process is associated with heavy conditions like temperature and pressure created for catalyst reactors. At that time, I gained some knowledge about centrifugal, reciprocating compressors, air-cooling apparatus, and high-pressure valves design.”
This led to his current role with Ruhrpumpen.
Identifying Technical Problems During Commissioning
There are three main groups of stages where technical problems can be raised, Kirill said.
1. Design stage.
“Some features of transported medium could be unknown or hidden from the eyes of engineers,” he explained. “Under operation, it can affect wearing, clogging, cavitation. etc. Liquid parameters like pressure and temperature could be changed due to process modernization or change in fact. Liquid chemical composition can vary during operation. Essentially, it relates to the oil industry where a refinery could get oil from one petroleum deposit, and after it can come from another.”
Also during this stage, corrosion and erosion agents can be a separate topic for evaluation. There are many articles and books which can recommend materials for appropriate materials application, Kirill said. “Practically, it’s better to rely on materials which are already used in each specific service. It comes from end user practice gained during operation of many plants in different locations, with special sources and in varied conditions.”
The design of piping is connected to the specific valves and pumps, he continued. “It’s very important to evaluate as there can be bottlenecks like vapor locks, dead legs, etc. Also, the design of pits, vessels for vertical pumps, is an essential topic and described basically in the standard of the Hydraulic Institute.”
Ambient conditions also come into play. For example, winter time and arctic regions, seismicity, sand storms, and glacier movement. The monitoring and control systems are mostly in dependent upong this process-importance status.
“Harmful effect is a major part of evaluation if you consider the negative impact to personnel,” he explained. “It can be noise features delivered from the pump. Or it can be metals contained in pump materials which can collect a nuclear radiation, if it’s nuclear industry equipment. Non-asbestos gaskets are mostly used for sealing pumps and valve joints. For this stage a piece of advice is to know about such conditions and requirements from the beginning.”
2. Site Construction and Installation
All goods supplied to customer’s site should be checked technically before being accepted, he suggested. “During transportation, equipment can be damaged or be in inappropriate conditions. When it comes to the customer, whether it’s a check list or the manufacturer’s manual, it will help to find out about problems with valves or pumps in advance. Foundation works are very important as proper filling of anchors holes and the frame itself by concrete will lead to the long life of dynamic equipment. There’s a tip about the consistency of concrete—there shouldn’t be any rubbish or exceeded quantity of water in it. In this case, the anchor can be rotated around its axis or move under by tapping it by a small hammer. It should be checked while framing the installation.”
During erection, appropriate tools and measures should be used, Kirill said. This information can be available in the equipment manual or its standard or industry regulation. For example, centrifugal API pump installation is in compliance with API 686. Hydraulic Institute, ISO, DIN, ANSI and manufacturer standards also define some specific requirements for these works. In some cases, industry regulations can be more stringent than the pump or valve manufacturer manual.
“Very important topics to consider are the pump baseplate alignment and horizontal positioning,” he said. “This should be checked by level/construction instruments. After these works are completed, anchor bolts are tightened with a pull-force gauge. After the piping is connected to the pump, the next step is to check the parallelism of pipes flanges and its gap. These values are indicated in the pump manual or documents listed above. If these parameters are exceeded, then high loads will be transferred to the pump, which will cause vibration and shutdown.”
It is customary during many installations for different materials to be used for pump flanges and pipes. “Mostly it’s connected with different grades of steels of castings and rolled products,” he said. “Methods of production are varied for pipes and accessories like pump and valves. In such cases it is recommended that flanges joints shall be from the same or closest possible materials. After welding is done, all qualification documents and laboratory tests shall be issued to operating personnel. If the wrong welding is made, then the weld joint will be damaged under different thermal expansion (where operating temperature is high) and lack of homogeneity.”
3. Commissioning & Start-Up
This stage is the final one before equipment is put into continuous operation. “This step shows the precision of production of the delivered pumps and valves. That’s why it is a major stage for the examining of erected equipment and utilities–lube oil station, water cooling and heating lines, electricity, control systems, and process lines.”
In the next step, the lube oil systems are installed, and interconnecting piping cleaned and put in place. “During commissioning, it is useful to operate with flowing oil to the pump bearings inlets (plugged) and via bypass line to back to oil reservoir,” Kirill explained. “During the re-circulation of oil, strainers are to be checked and cleaned in a timely manner, so the entire system would be free of solids and contaminants. Instruments will show the correct values. Water cooling and heating lines can be with the weld hearth cinder. So these utilities must be re-circulated by the appropriate agent via temporary filters, as well in order to clean up whole system.”
Electricity wires are to be erected and started to all consumers including e-motors, instruments, lighting and etc. “First, all electrical drivers must be disconnected from process equipment, which can’t run in ‘dry’ conditions,” he said. “For most valves it is possible without disconnecting from their motors. Drivers are in operational conditions and equipment is pre-aligned, anchors are tightened, couplings are disassembled where needed, preservation is removed, and the system and bearings are lubricated.”
Then the control system is connected and switched on.
“At this stage all pumps and valves are to be clean from solid contaminants, bearings are filled by grease or oil, the seal system is filled by barrier fluid,” he explained. “It’s time to fill the pump and valve with fluid for commissioning. It is recommended that filling is made from the suction/inlet line via recommended installed temporary strainers. Then pumps can be started for re-circulating fluid via all process lines and back to the pumps. Strainers are to be checked and cleaned in a timely manner. Issued parameters from instruments should be checked for compatibility.”
At this point, the whole system is ready to be launched. “We need to remember that commission conditions differ from operational (pressure, temperature and other features of fluids). Therefore, for pumps it is important to re-check alignment during start-up by changing operating and standby pumps.”
Maintenance and Safety Tips for Pumps and Valves
Kirill suggested using the manufacturer’s manuals as primary guides.
“In common operations, the engineer should have all the documentation, including an oil re-fill schedule,” he recommended. “The maintenance schedule should be prepared and kept in an observed place. Additionally, it is useful to have a notebook for repairs which will allow for the collection of data. Analyses will help engineers gain knowledge about how to change such situations or be ready to them.”
Kirill said that pumps and valves should be:
heated during standby for high temperature service
observed timely for checking oil, seal systems and all connected utilities
electrically heated when ambient temperature is below the fluid pour point or case design temperature
shaft should be rotated during standby where it’s required.
With regard to safety, personnel should wear suitable working clothes. Safety glasses can protect from leakages and other relative sweeping. “Leakages from a high-pressure line (over 150 bar pressure) can pass through the pump flange connection and be very destructive, even it trickles,” Kirill said.
“All dynamic equipment causes noise which shall be evaluated to consider frequency of personnel being near the equipment. Therefore, earphones can be a reliable protection from its harmful impact. Safety gloves and helmet are obligatory things. Pump and valve rotating parts which are exposed to personnel access must be covered by safety guard.”
If repair is required on a stopped pump or valve then it must be plugged from lines under operation, he said. “Equipment is to drained, steamed and cooled down to ambient temperature. All required tools are to be integral and safe.”
For young end users the best advice, Kirill said, is to try to communicate with colleagues from their industry. “Some of them will be of different age, closed, or without good skills for teaching, but in any way if young people accompany/support them during work, it will bring more knowledge and experience rather than if they would try to gain this information from books and manuals. Please value other people.”
Michelle Segrest is president of Navigate Content, Inc., a full-service content creation firm, and has been a professional journalist for more than three decades. She has covered the industrial processing industries since 2008 and specializes in technical articles and case studies that focus on technology and innovation connected with rotating equipment. michelle@navigatecontent.com